Guide to Plastic Resin
Bottles used in medical industry are generally made from plastics. The plastics are mainly categorized in 5 types- Polyethylene (PE), Polypropylene (PP), Ethylene-Vinyl Alcohol Copolymer (EVOH), Poly-Vinyl Chloride (PVC) and Polyethylene Terephthalate (PET).
Let us know the difference between the various types of plastics.
- Polyethylene (PE) – Polyethylene has lower specific gravity, chemical stability and water and chemical resistance. It has an excellent strength and flexibility. PE is classified into –
- HDPE (PE-LD, High Density Polyethylene): Has excellent water and chemical resistance and relatively high resistance to hot and cold temperatures.
- LDPE (PE-LD, Low Density Polyethylene): Has excellent flexibility, and water and chemical resistance.
- LLDPE (PE-LLD, Linear Low Density Polyethylene): Has higher tensile strength and cold temperature resistance.
- Polypropylene (PP) – Polypropylene has superior rigidity, heat resistance, and water and chemical resistance.
- Ethylene-Vinyl Alcohol Copolymer (EVOH) – EVOH has an excellent gas barrier performance to oxygen and also provides high flavor protection and high oil and abrasion resistance.
- Polyethylene Terephthalate (PET) – It provides higher heat resistance, transparency and strength, and can be used for various purposes.
- Polyvinyl Chloride (PVC) – Itis naturally clear, has extremely good resistance to oils, and has very low oxygen transmission. It provides an excellent barrier to most gases and its drop impact resistance is also very good. This semi-rigid material is also very chemically resistant, but it is vulnerable to solvents.
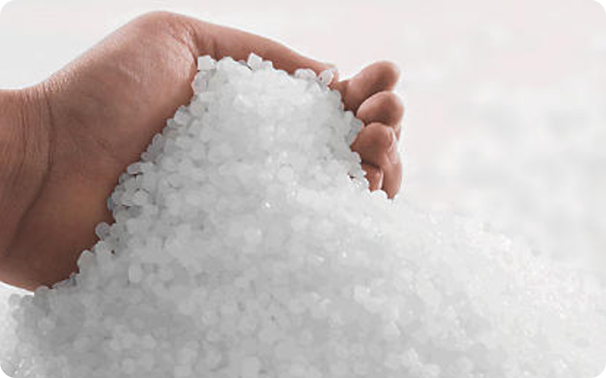
CRC
Child resistance closure is a special safety cap used to reduce the risk of children ingesting dangerous items including over the counter medications, pesticides, household chemicals etc.
A history of accidents involving children opening household packaging and ingesting the contents led the U.S. Congress to pass the Poison Prevention Packaging Act of 1970, authored by U.S. Senator Frank E. Moss of Utah. This gave the U.S. Consumer Product Safety Commission the authority to regulate this area. Additions throughout the decades have increased the initial coverage to include other hazardous items, including chemicals regulated by the Environmental Protection Agency. Coordination exists for improving international standards on requirements and protocols
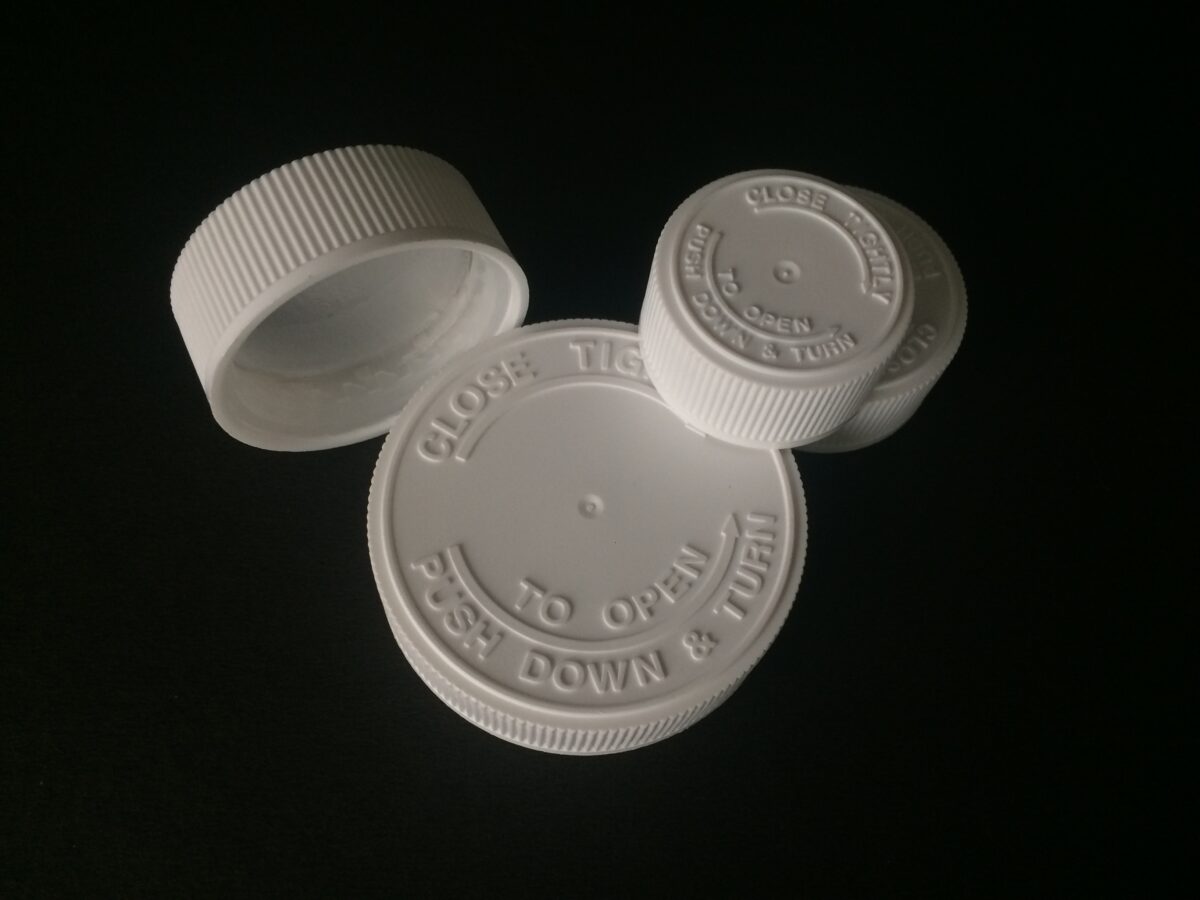
Screw Caps
A screw cap or closure is a common type of closure for bottles, jars, and tubes. A screw closure is a mechanical device which is screwed on and off of a “finish” on a container. Either continuous threads or lugs are used.
It must be engineered to be cost-effective, to provide an effective seal (and barrier), to be compatible with the contents, to be easily opened by the consumer, often to be re-closable, and to comply with product, package, and environmental laws and regulations.
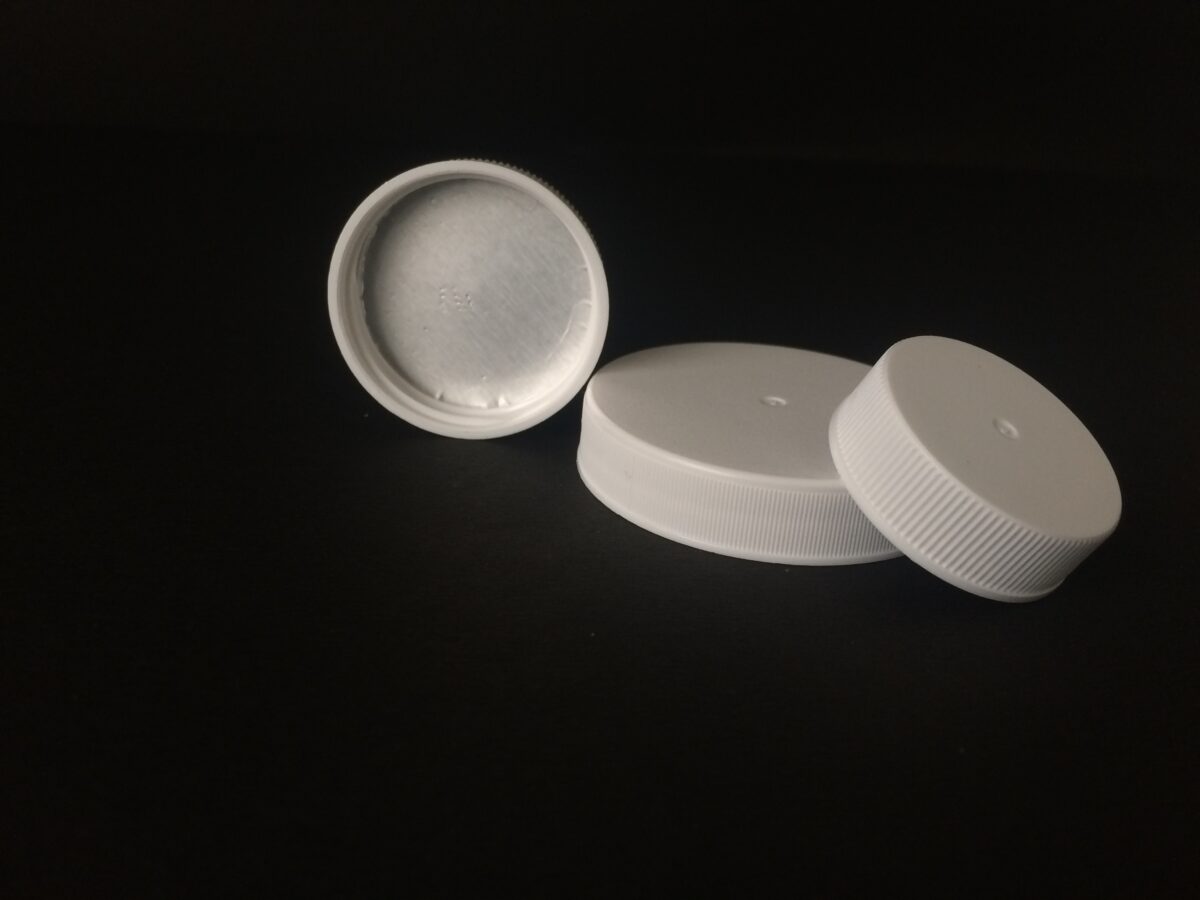
Quality Testing
Containers-
- Leakage test: Fill ten containers with water. Fit with intended closures and keep tem inverted at room temperature for 24 hour. There are no signs of leakage from any container.
- Collapsibility Test: This test applicable to containers which are to be squeezed in order to remove the contents. A container by collapsing inwards during use yields at least 90% of its nominal contents at the required rate of flow at ambient temperature.
- Clarity of aqueous extract: Select unlabelled, unmarked and non-laminated portions from suitable containers, taken at random sufficient to yield a total area of sample required taking into account the surface area of both sides Cut these portions into strips none of which has a total area of more than 20 cm2. Wash the strips free from extraneous matter by shaking them with at least two separate portions of distilled water for about 30 seconds in each case, then draining off the water thoroughly.
- Transparency test: Fill five empty containers to their nominal capacity with diluted suspension as described in IP 1966. The cloudiness of the diluted suspension in each container is detectable when viewed through the containers as compared with a container of the same type filled with water.
- Water vapor permeability test: Fill five containers with nominal volume of water and heat seal the bottles with an aluminum foil-poly ethylene laminate or other suitable seal. Weigh accurately each container and allow standing (without any overwrap) for 14 days at a relative humidity of 60+5% and a temperature between 20 and 25 0C reweigh the containers. The loss in weight in each container is not more than 0.2%.
Closures-
- Penetrability: This is measured to check the force required to make a hypodermic needle penetrate easily through the closure. It is measured by using the piercing machine. The piercing force must not exceed a stated value. If it exceeds that stated value, the hypodermic needle can be damaged as a result of undesirable hardness of the closures.
- Fragmentation test: This test is performed on 20 closures. Each closure is penetrated with hypodermic needle in a piercing machine five times within a limited area and needle is washed to transfer any fragment present. The contents are filtered through coloured paper that contrasts with the rubber and the fragments counted. On an average there should not be more than three fragments per unit.
- Self-sealability test: Applicable to multidose containers fill 10 vials with water close them with prepared closures and secure with a cap. For each closure use a new hypodermic needle and pierce 10 times each time at different site immerse the vials upright in methylene blue (0.1%) solution and reduce external pressure for 10 minutes. Restore the atmospheric pressure and leave the vials immersed for 30 minutes. Rinse the outside of the vials. None of the vials contains any trace of coloured solution.
- Extractive test: In this test, the closure is boiled with water for four hours under reflux and the water evaporated to dryness. The residue must not exceed the specified amount.
- Compatibility test: This test is performed to check the compatibility of the rubber closures with various types of the substances, since it is necessary to ensure that there is no interaction between the contents of the bottle and the closure.
- Light absorption: Filter solution A through membrane filter. Measure the light absorbance of filtrate in the range 220 to 360 nm using a blank solution (prepared in the same manner as solution A). The absorbance is not more than2.
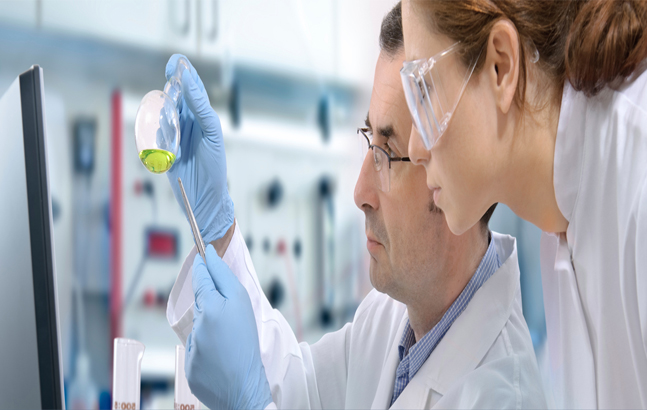
Closure Guide
The application torque of closures must be controlled in order for the closures to perform properly in the field. Closures must be applied tight enough to maintain a seal and to resist closure back-off, but must be not be applied so tightly that the end user cannot remove the closure.
Neck Finish | Inch-Pounds | Newton-Meter |
8 | 3-7 | 0.34-0.79 |
10 | 4-8 | 0.45-0.90 |
13 | 5-9 | 0.56-1.02 |
15 | 5-9 | 0.56-1.02 |
18 | 7-10 | 0.79-1.13 |
20 | 8-12 | 0.90-1.36 |
22 | 9-14 | 1.02-1.58 |
24 | 10-18 | 1.13-2.03 |
28 | 12-21 | 1.36-2.37 |
30 | 13-23 | 1.47-2.60 |
33 | 15-25 | 1.70-2.82 |
38 | 17-26 | 1.92-2.94 |
43 | 17-27 | 1.92-3.05 |
48 | 19-30 | 2.15-3.39 |
53 | 21-36 | 2.37-4.07 |
58 | 23-40 | 2.60-4.52 |
63 | 25-43 | 2.82-4.86 |
66 | 26-45 | 2.94-5.09 |
70 | 28-50 | 3.16-5.65 |
83 | 32-60 | 3.62-6.78 |
86 | 40-65 | 4.52-7.34 |
89 | 40-70 | 4.52-7.91 |
100 | 45-70 | 5.09-7.91 |
110 | 45-70 | 5.09-7.91 |
120 | 55-95 | 6.21-10.73 |
132 | 60-95 | 6.78-10.73 |
Resin Comparison Chart
There are various properties of different types of resins which need to be understood before purchasing any plastic container. The physical properties of resins, their permeability to different substances and their resistance to different substances differ to great extent.
Properties | PET Oriented | PET Unoriented | PETG | PVC Unoriented | HDPE | LDPE | PP |
Clarity | Clear + | Clear + | Clear + | Clear | Translucent | Translucent+ | Translucent+ |
Scuffing Resistance | poor/fair | poor/fair | fair | good | very good | very good | very good |
Impact Strength | good to | poor to | poor to | fair to | good to | excellent | poor to good |
excellent | fair | fair | good | excellent | |||
Stiffness | moderate | moderate | moderate | moderate | moderate | low | moderate |
to high | to high | to high | to high | to high | |||
Maximum Hot Fill* | 120°F | 140°F | 140°F | 140°F | 180°F | 150°F | 240°F |
PERMEABILITY TO: |
S.P.I. Specifications for neck of the container
The threads in the neck and the dimensions of the neck decide the size of the closure to be used. So we must have a clear idea about the neck finishes. There are some common S.P.I specifications which must be considered
- “H” Dimension: The height of the neck finish. Measured from the top of the neck to the point where the diameter “T”, extended down, intersects the shoulder.
- “S” Dimension: Measured from the top of the finish to the top edge of the first thread. The “S” dimension is the key factor which determines the orientation of the closure to the bottle and the amount of thread engagement between the bottle and cap.
- “I” Dimension: The inner diameter of the bottle neck. Specifications require a minimum “I” to allow sufficient clearance for filling tubes. Liner less closures, with a plug or land seal, and dispensing plugs and fitments require a controlled “I” dimension for a proper fit.
- “T” Dimension: The outside diameter of the thread. The tolerance range of the “T” dimension will determine the mate between bottle and closure.
- “E” Dimension: The outside diameter of the neck. The difference between the “E” and “T” dimensions divided by two determines the thread depth.

Resin Recycling Code System
The primary purpose of the codes is to allow efficient separation of different polymer types for recycling. Separation must be efficient because the plastics must be recycled separately. Even one item of the wrong type of resin can ruin a mix. Let us have a review at those –
- PETE, or PET, (Polyethylene Terephthalate) is the most commonly recycled plastic. It is used in the manufacturing of recyclable plastic containers, soft drink bottles, and oven-safe trays. Recycled PET products include: carpeting, fiberfill, unsaturated polyester, urethane foam, strapping, engineering plastics, and extruded products
- HDPE (High Density Polyethylene) is used to make milk jugs, base cups of plastic soda bottles, toys, luggage, and heavy-duty trash bags. 50-60% of all bottles are made of HDPE. Recyclable HDPE can be used in soft drink base cups, plastic lumber, containers, drums, pails, and pipes.
- PVC (Polyvinyl Chloride) is commonly used to make credit cards, garden hoses, records, food wrap, and cooking oil bottles. Recycled PVC products include sewer pipes, telephone cables, window frames, down spouts, flower pot covers and office accessories.
- LDPE (Low Density Polyethylene) is used to make bags, disposable diaper backings, stretch wrap, and milk jug lids. Recycled LDPE can be used to create containers, house/office supplies, pipe, construction material, fiber, and playground equipment.
- PP (Polypropylene) is the plastic material most commonly used for straws, syringes, dairy tubs, small appliances and carpet backing. Recycled PP can be used to make auto battery cases, carpet backing furniture and video cassette containers.
- PS (Polystyrene) is used to manufacture containers used by the fast food industry, plastic silverware, test tubes, and C/D cases. PS in fast food products can be recycled into office supplies, video cassette boxes, and other products. When combined with other plastics, PS can be turned into plastic lumber for walkways, benches, and packing materials.
- Other- This category is comprised of any resin not covered in 1-6 and plastics which are a combination of resins. The other category sometimes appears in microwavable serving ware and food containers. It may be recycled into benches, picnic tables, roadside posts and marine pilings.
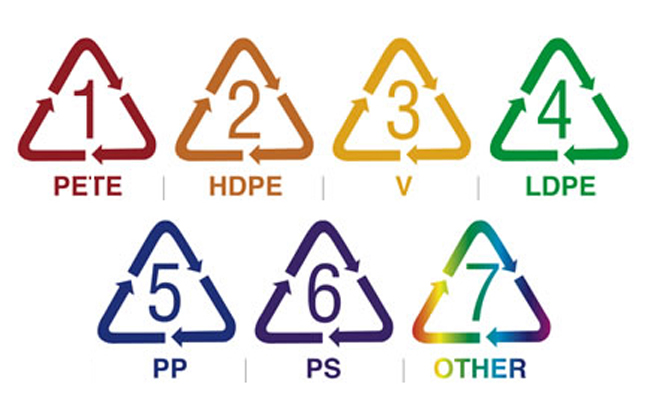
Anatomy of Bottle
Let us know the anatomy of the bottle-
- Mouth-It is the opening of the bottle.
- Bead- It is the finish line of neck where the cap of the bottle rests.
- Threads- These are spirals on the neck onto which the closures are twisted.
- Neck Finishes-The part of the bottle which holds the closure.
- Standard Capacity- The normal value measured in cc’s or ml’s on the bottles, published in standard sizes used by the industry.
- Shoulder- It is the sloped area between the neck and the body of the bottle.
- Overflow capacity- It is the capacity of the bottle after which the content will overflow.
- Base- The bottom area of the bottle often marked with resin identification code.